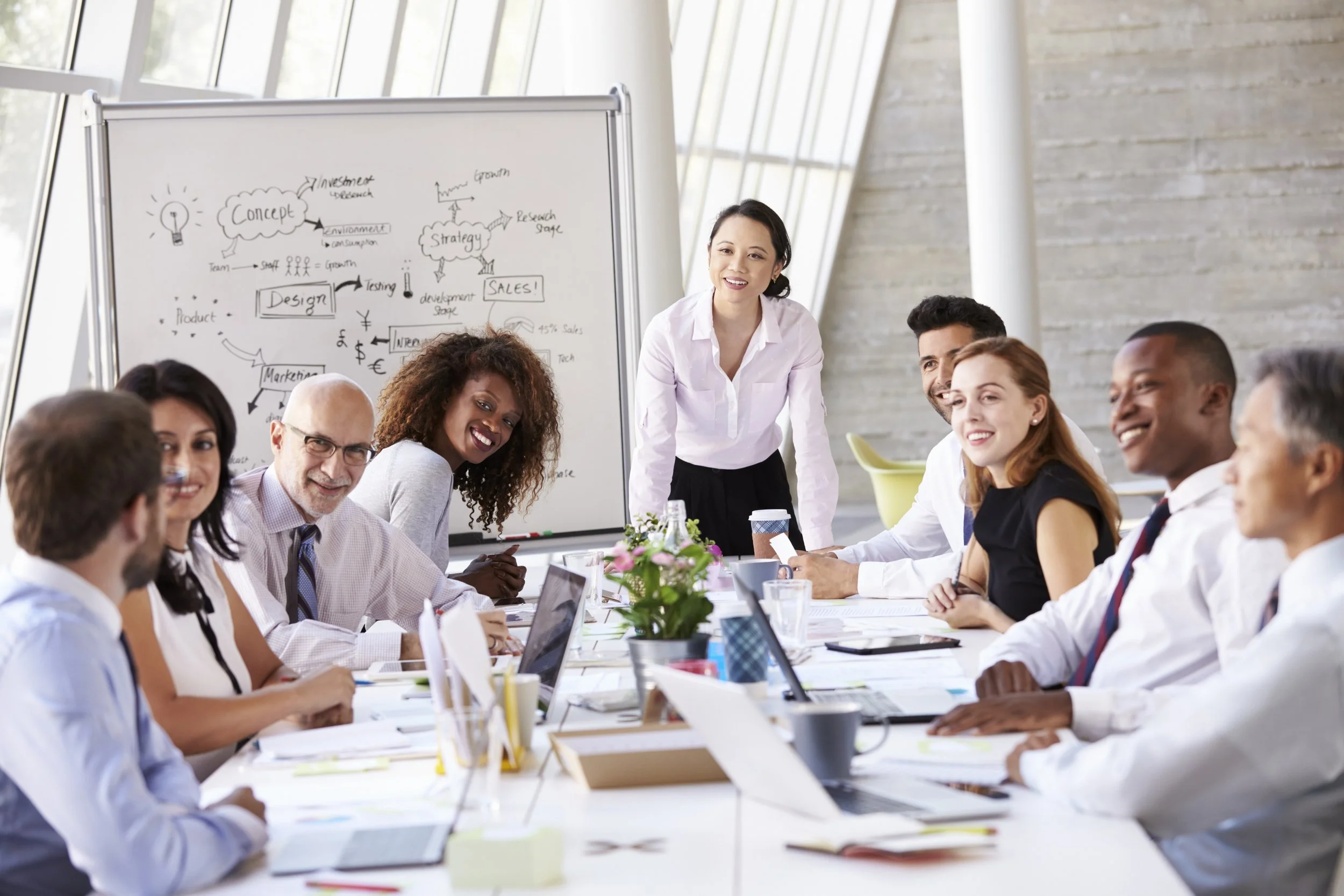
Total Cost of Ownership
Stop relying on PPV or FOB Landed as the measure of profitability. Instead, use HermitCrab's TCO Advisory Services to make informed decisions on which products should be brought back to the US for production. Our TCO tools consider at least 25 unique variables to help confirm your reshoring decision.
Why Reexamine TCO?
The world has changed. A lot! Those changes affect the traditional methods of determining the cost of manufacturing goods in the US versus "low cost countries". It's time to consider all the factors that drive the cost of goods, not just wages.
For far too long, large retail and distribution enterprises have focused on landed costs and purchase price variance to determine which products should be made offshore. Many of these decisions were made decades ago, during the peak of globalization when geopolitical stability was assured. Not only are those days gone, but the current environment for global supply chains is evolving rapidly, and not for the better.
HermitCrab believes that our customers can successfully identify and relocate product manufacturing to the U.S. by taking into account the complete and total cost of ownership. This comprehensive approach includes not only direct financial costs but also considers non-hard dollar factors such as ESG (Environmental, Social, and Governance) criteria and geopolitical stability. By doing so, enterprises can make an informed choice about what should be brought back to the U.S., ensuring sustainability and resilience in their manufacturing strategies.
What are the Top 10 Factors to Consider for TCO Calculations?
1) Labor Costs: Labor costs include wages, overtime, and benefits such as healthcare and retirement plans. In the U.S., labor expenses are typically higher due to minimum wage laws and more extensive benefit requirements. Conversely, many Asian countries offer cheaper labor costs, but this can come with trade-offs in terms of worker turnover and skill levels.
2) Raw Material Sourcing: The availability and cost of raw materials can vary greatly between regions. In some Asian countries, certain materials may be more readily available, leading to lower costs and shorter lead times. On the other hand, the U.S. might offer higher quality raw materials at a higher price but with more predictable supply chains.
3) Quality Control and Assurance: Maintaining consistent product quality can incur different costs depending on the geographic location. The U.S. typically has stringent quality standards that might increase operational costs but ensure better reliability. In Asia, quality control measures might be less costly but could require additional oversight and potential rework costs.
4) Shipping and Logistics: Logistics encompass transportation fees, warehousing, and handling costs from the manufacturing site to the final destination. Shipping from Asia to the U.S. can be expensive and time-consuming, with risks of delays. However, domestic manufacturing in the U.S. reduces transportation costs and lead times, making the supply chain more responsive.
5) Tariffs and Taxes: Importing goods from Asia to the U.S. can incur significant tariffs, which add to the total landed cost. Taxes, including value-added tax and customs duties, can also vary and impact the overall expense. Manufacturing domestically helps avoid these extra charges but still involves local state and federal taxes.
6) Compliance and Regulatory Costs: Compliance with local laws on environmental standards, safety regulations, and labor laws can be costly. The U.S. has strict regulations that can increase operational expenditures. Asian countries might have less stringent regulations, but non-compliance can lead to heavy fines and disruptions.
7) Overhead Costs: Overhead costs include utility expenses, property leases, and administrative salaries. Industrial real estate and energy costs can be higher in the U.S., increasing overall operational expenses. Conversely, lower overhead costs in some Asian countries can offer a significant cost advantage.
8) Exchange Rates: Fluctuations in currency exchange rates can affect the cost of purchasing materials and paying for labor. A weaker dollar can make importing goods from Asian countries more expensive. Manufacturing in the U.S. eliminates currency risk but might miss out on potential savings from favorable exchange rates.
9) Operational Risks: Political stability, economic conditions, and susceptibility to natural disasters all contribute to operational risks. The U.S. offers a relatively stable political and economic environment, minimizing these risks. Some Asian countries might experience higher political unrest or natural calamities, which could disrupt operations and increase costs.
10) Intellectual Property Protection: Protecting intellectual property (IP) is crucial to avoid unauthorized use or replication of products. The U.S. has strong IP laws and enforcement mechanisms, which can raise costs but ensure robust protection. In contrast, weaker IP laws in some Asian countries could lead to higher risks of IP theft, leading to potential long-term costs.
11) (Bonus!) Environmental, Social and Governance: The emergence of ESG over the last few years adds a distinct advantage to bringing manufacturing back to the United States. Costs and benefits related to sustainable practices, social responsibility, and governance standards, such as reducing carbon footprint, fair labor practices, and ethical business conduct, place the US far ahead of China, India, and the rest of Asia. Making a product in the US reduces the Supply Chain carbon footprint of a container of goods by 95%.